- Residential Furniture
- Dining Room Furniture
- Kids’ Furniture
- Living Room Furniture
- Office Furniture
- Mattress
- Pet Furniture
- Outdoor furniture
- Hotel Furniture
- Multi-Functional Furniture
- Multi-functional Upholstered Sofa
- School Furniture
- Specialty Furniture
- Study Room Furniture
- Public Furniture System
- Smart Furniture
Winning Long-Term Orders in Global Furniture Trade: The “Zero-Defect”
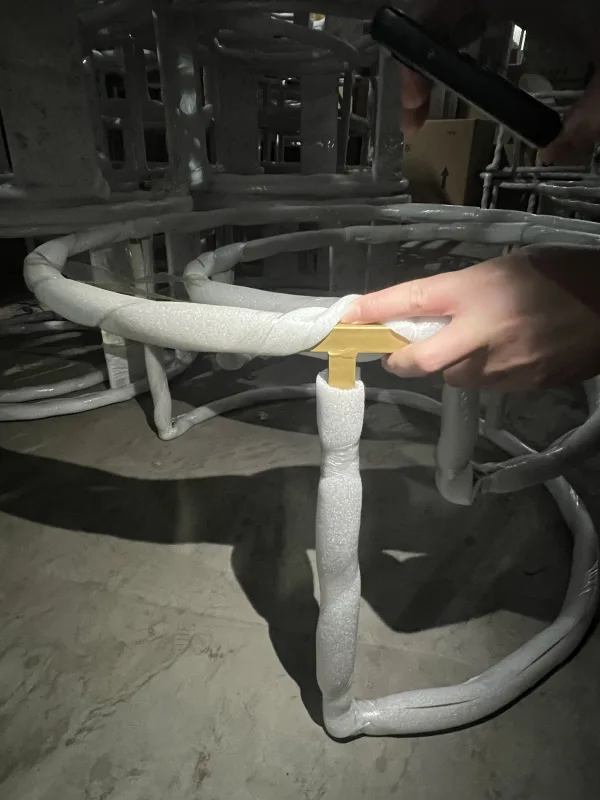
In today’s fiercely competitive global furniture market, client priorities have shifted from “cost-performance” to zero-defect quality. To secure sustainable orders, exporters must adopt rigorous quality control as their shield. This article reveals how furniture trade enterprises can leverage uncompromising standards to dominate the international arena.
Quality Control System: A Closed-Loop Process from Raw Materials to Finished Products
Source Control
•
Key indicators such as wood moisture content and metal fittings’ corrosion resistance must comply with the standards of the target export country.
•
Sign “Quality Joint Liability Agreements” with suppliers to ensure full traceability of raw materials
Production Standardization
•
Implement a quality management system, with inspection checkpoints at each production stage (e.g., mortise-tenon joint precision, paint adhesion tests).
•
Adopt a dual-mechanism of “first-article inspection + batch sampling” to mitigate risks of large-scale rework.
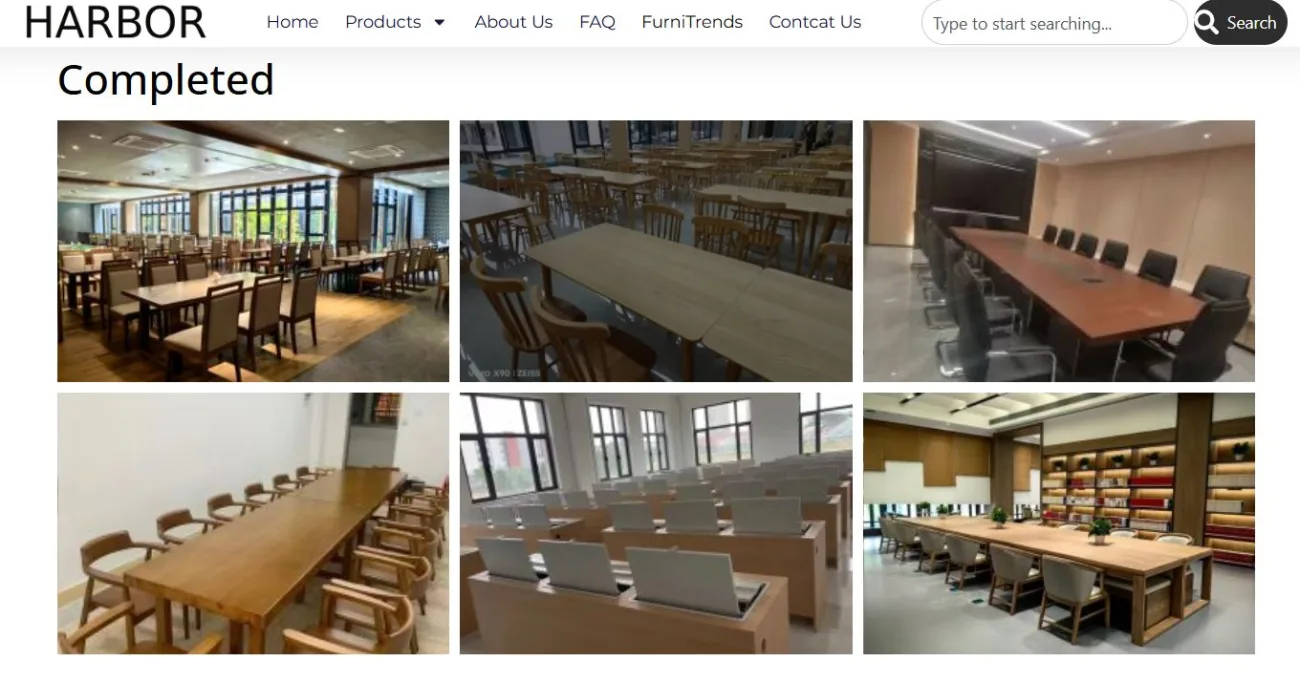
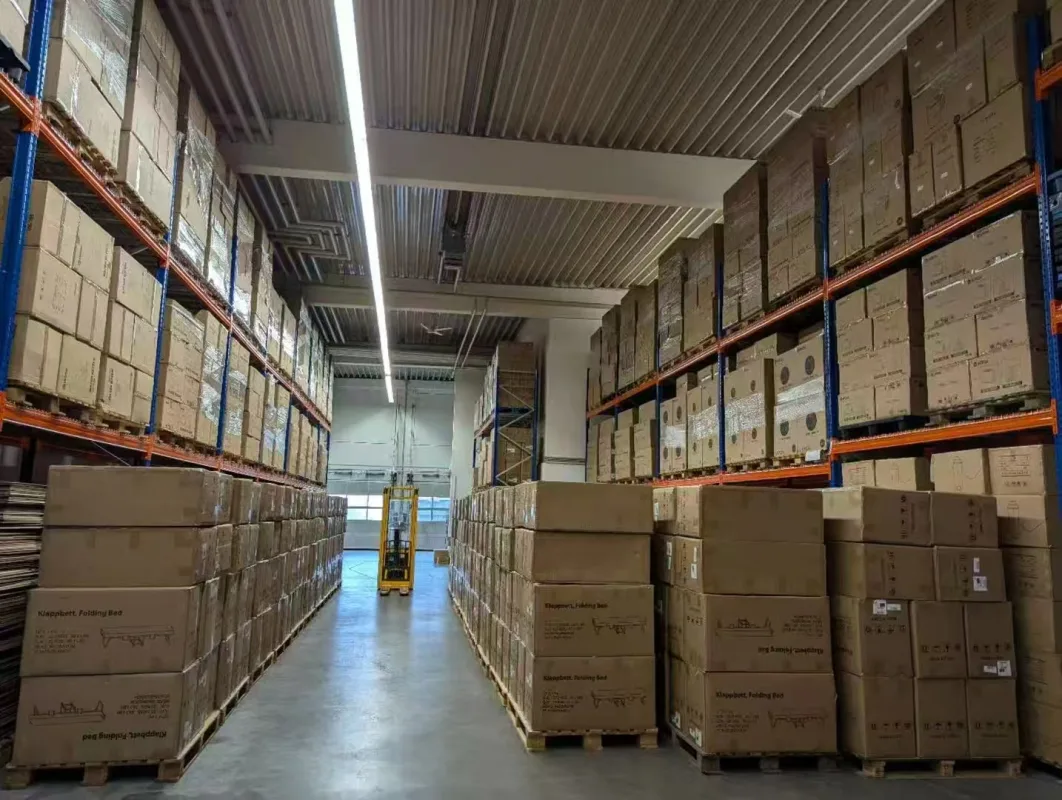
Quality Control Upgrades Driven by Customer Pain Points
Transportation Adaptability:
Simulate maritime shipping vibration tests to ensure packaging pressure resistance; offer “damage-free delivery” insurance services.
Cultural Adaptation:
Customize inspection checklists based on regional preferences—e.g., heavyweight styles for Middle Eastern clients and minimalist designs for Nordic customers.
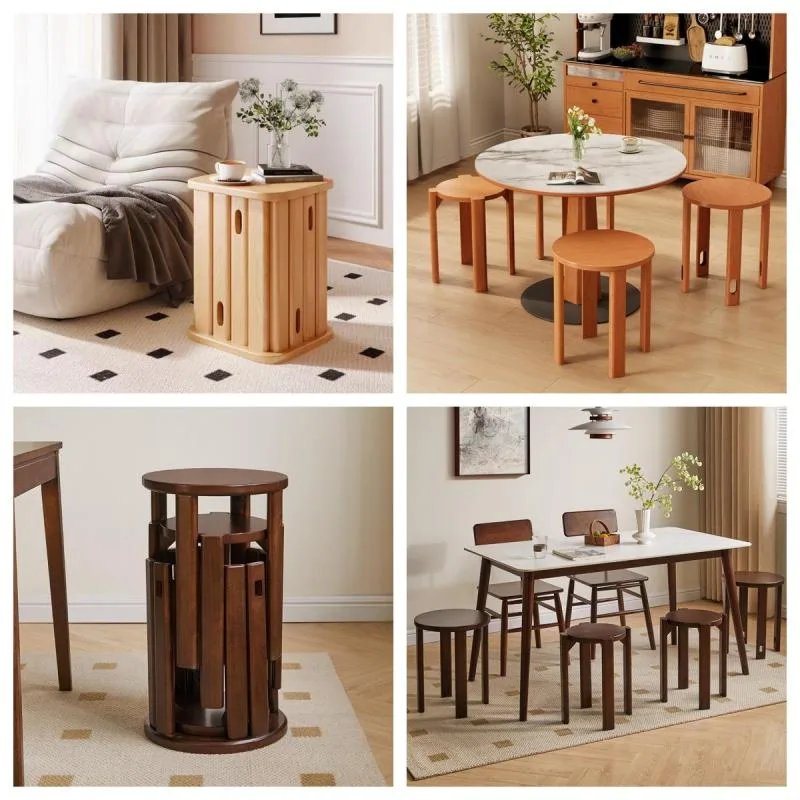